Thin Film Production
Physical Evaporation System (PVD)
VAKSİS 1M4T PVD
Using 4 efussion furnaces, it can reach temperatures up to 1300 °C and using 1 RF and 1 DC sputtering system, conductive and insulating materials can be evaporated and desired coating can be made on the substrates. The coating thickness deposited on the substrate can be controlled with five thickness monitors. In addition, the sample to be coated on the horizontal axis can be rotated.
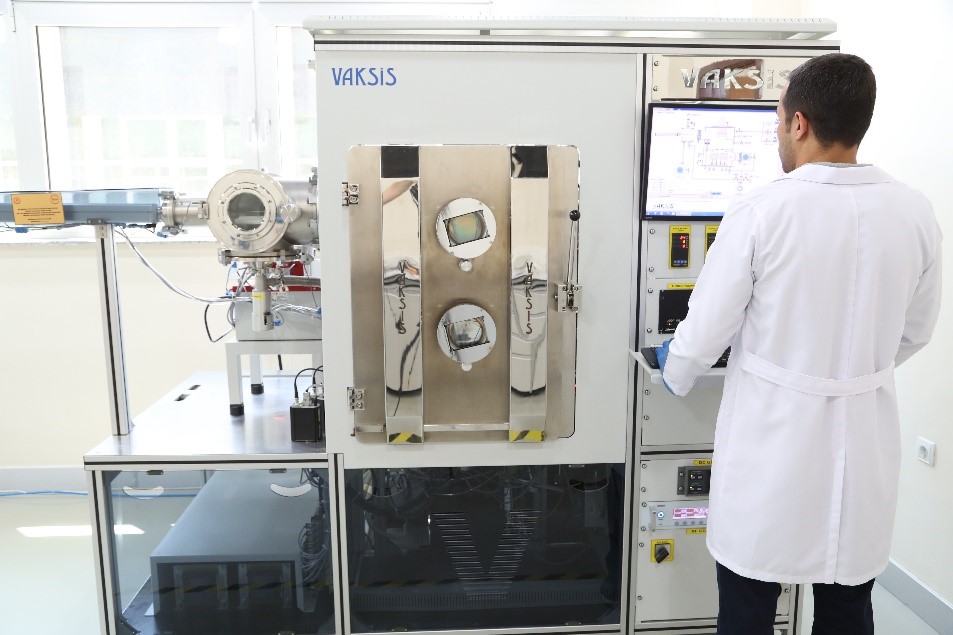 |
- The system can go down to 1 x 10-7 Torr vacuum level
- It has LN2 “cold finger”
- It has a circular sample area with a diameter of 15 cm
- It has a sample rotation speed of 3 - 30 rpm
- It has 500 °C sample-substrate heating and ±1 °C temperature control.
- There are 10 VAC x 300A, 3000 Watt AC, four channel co-evaporation power supplies
- It has five channels, thickness measurement and control unit
- Organic material can also be evaporated using suitable ceramic crucibles
- It has sputtering head of 2.5 inch
- It has a 300 Watt RF power supply and a 1500 Watt DC power supply
- Ar, N2 and O2 as gas lines contain
- The system can coat with ±5% thickness homogeneity for 15 cm diameter
|
Ultrasonic Spray Pyrolysis System (USP)
SONO-TEK Flexi Coat
It can spray all kinds of material solutions (including acidic and aggressive solutions) as well as materials such as CIGS and CIS at ultrasonic frequencies and also coat membrane interfaces for fuel cells. Coating can be done by reaching levels lower than 3% oxygen in the inert gas (nitrogen gas) media, by increasing the substrate temperature up to 500 °C.
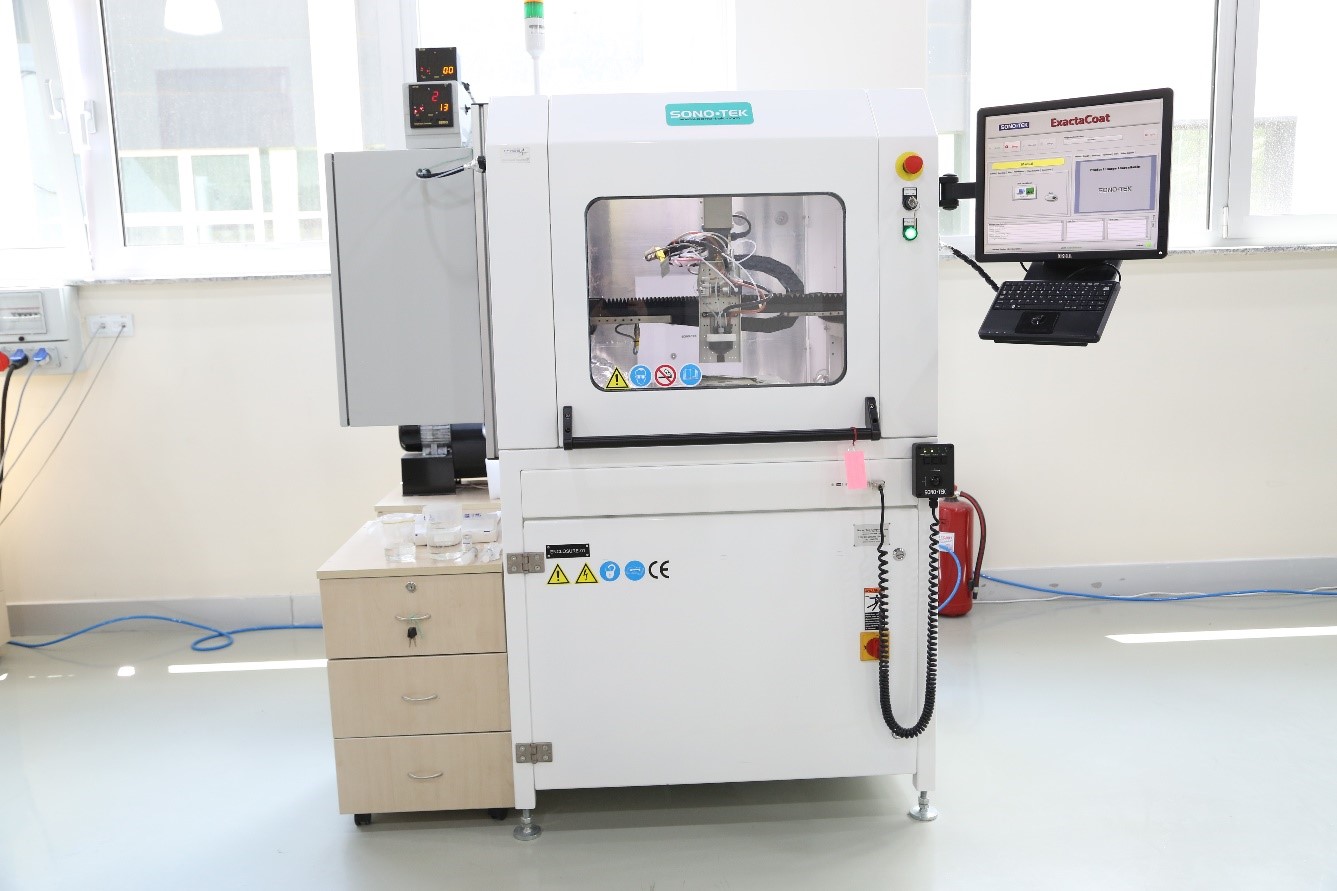 |
- Areas of 45 x 45 cm2 can be coated
- It has two ultrasonic probes, 120 kHz and 80 kHz
- The movement mechanism with nozzle connection can move in three dimensions as x, y and z
- Sample-substrate holder can reach up to 500 °C
- It can allow the desired coating from acidic solutions
- During the coating process, N2 inert gas is used to avoid undesirable chemical reactions, and thanks to N2 inert gas, the oxygen level is reduced below 3%
|